What is Porosity in Welding: Important Tips for Achieving Flawless Welds
Wiki Article
Porosity in Welding: Identifying Common Issues and Implementing Best Practices for Avoidance
Porosity in welding is a pervasive concern that usually goes undetected up until it triggers significant troubles with the honesty of welds. In this discussion, we will check out the essential elements contributing to porosity development, examine its damaging results on weld performance, and review the best practices that can be adopted to minimize porosity event in welding procedures.Common Reasons of Porosity

Another constant wrongdoer behind porosity is the visibility of pollutants on the surface area of the base steel, such as oil, oil, or rust. When these pollutants are not effectively gotten rid of before welding, they can vaporize and come to be entraped in the weld, triggering defects. In addition, utilizing dirty or damp filler materials can present impurities into the weld, adding to porosity concerns. To alleviate these common reasons for porosity, complete cleansing of base steels, proper shielding gas selection, and adherence to ideal welding specifications are necessary techniques in achieving top quality, porosity-free welds.
Effect of Porosity on Weld Top Quality

The existence of porosity in welding can considerably jeopardize the structural integrity and mechanical homes of welded joints. Porosity produces voids within the weld metal, damaging its total toughness and load-bearing capability.
Among the key repercussions of porosity is a decline in the weld's ductility and toughness. Welds with high porosity levels often tend to exhibit reduced impact strength and reduced capability to deform plastically before fracturing. This can be especially concerning in applications where the welded components go through dynamic or cyclic loading problems. Additionally, porosity can hinder the weld's capability to effectively transmit pressures, bring about premature weld failure and possible safety and security dangers in important structures.
Best Practices for Porosity Avoidance
To improve the structural stability and high quality of welded joints, what particular procedures can be carried out to lessen the incident of porosity throughout the welding process? Utilizing the appropriate welding method for the particular material being welded, such as adjusting the welding angle and weapon placement, can additionally stop porosity. Routine assessment of welds and instant remediation of any issues recognized throughout the welding process are necessary practices to stop porosity and produce top notch welds.Importance of Correct Welding Techniques
Carrying out correct welding strategies is extremely important in making certain the architectural honesty and top quality of bonded joints, constructing upon the structure of efficient porosity prevention steps. Welding techniques directly affect the total strength and longevity of the bonded structure. One vital element of proper welding strategies is maintaining the appropriate warmth input. Too much heat can bring about raised porosity because of the entrapment of gases in the weld pool. Alternatively, inadequate warmth may cause incomplete blend, producing potential weak factors in the joint. Additionally, making use of the suitable welding criteria, such as voltage, current, and take a trip rate, is crucial for attaining sound welds with minimal porosity.Additionally, the selection of welding procedure, whether it be MIG, TIG, or stick welding, ought to line up with the certain needs of the job to make certain ideal results. Proper cleansing and preparation of the base metal, in addition to choosing the appropriate filler material, are also crucial parts of proficient welding methods. By sticking to these ideal techniques, welders can decrease the danger of porosity formation and generate high-grade, structurally audio welds.
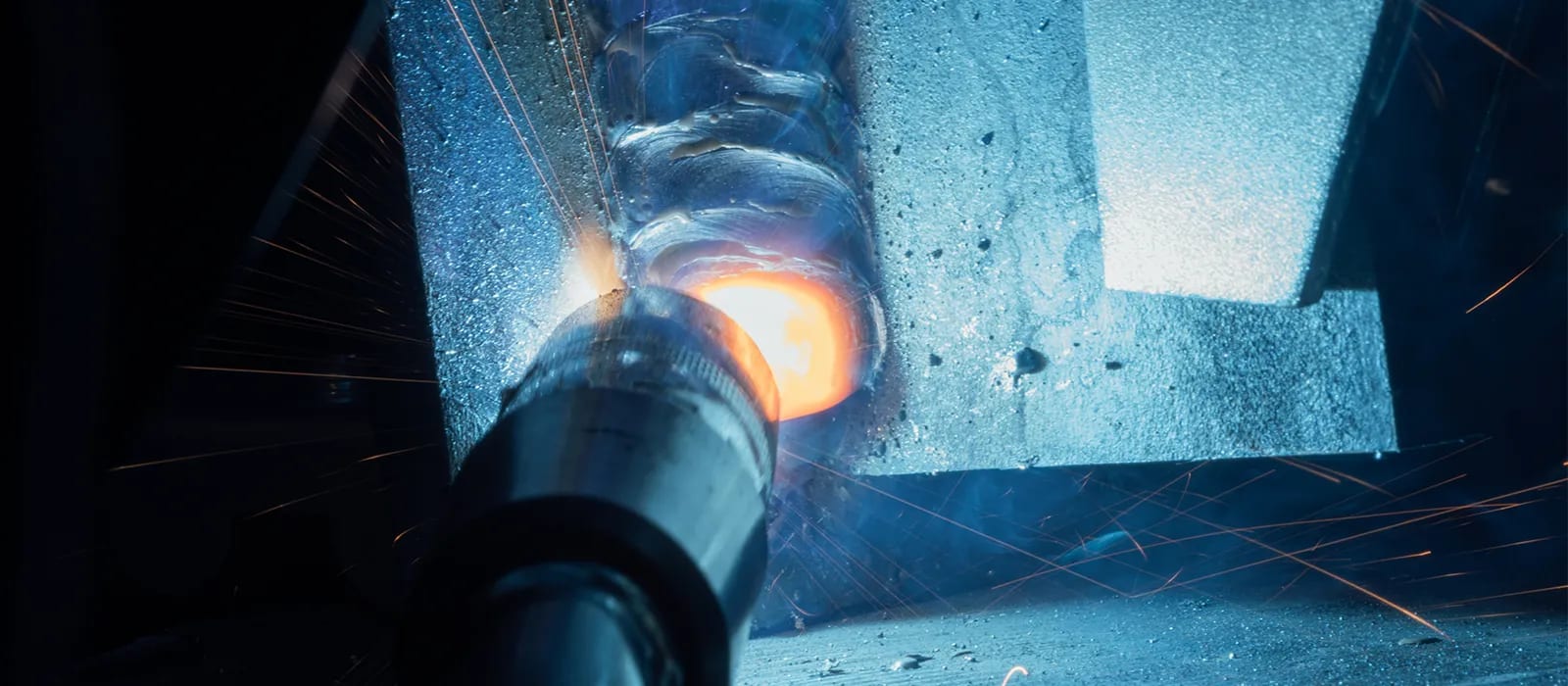
Examining and Top Quality Control Measures
Quality control procedures play an important duty in verifying the stability and dependability of bonded joints. Testing procedures are important to spot and stop porosity in welding, making certain the strength and longevity of the last product. Non-destructive screening methods such as ultrasonic screening, radiographic testing, and aesthetic evaluation are commonly utilized to identify possible problems like porosity. These strategies allow for the analysis of weld high quality without endangering the stability of the joint. What is Porosity.Performing pre-weld and post-weld assessments is likewise critical Homepage in keeping high quality control standards. Pre-weld examinations include validating the products, equipment setups, and cleanliness of the workplace to avoid contamination. Post-weld assessments, on the other hand, examine the final weld for any kind of problems, consisting of porosity, and confirm that it fulfills specified criteria. Executing a thorough high quality control strategy that includes complete testing treatments and inspections is vital to reducing porosity problems and making certain the overall top quality of welded joints.
Conclusion
In final thought, porosity in welding can be an usual concern that affects the top quality click site of welds. By identifying the common sources of porosity and carrying out ideal methods for avoidance, such as appropriate welding techniques and screening steps, welders can ensure premium quality go right here and reputable welds. It is necessary to focus on prevention approaches to reduce the event of porosity and preserve the honesty of welded frameworks.Report this wiki page